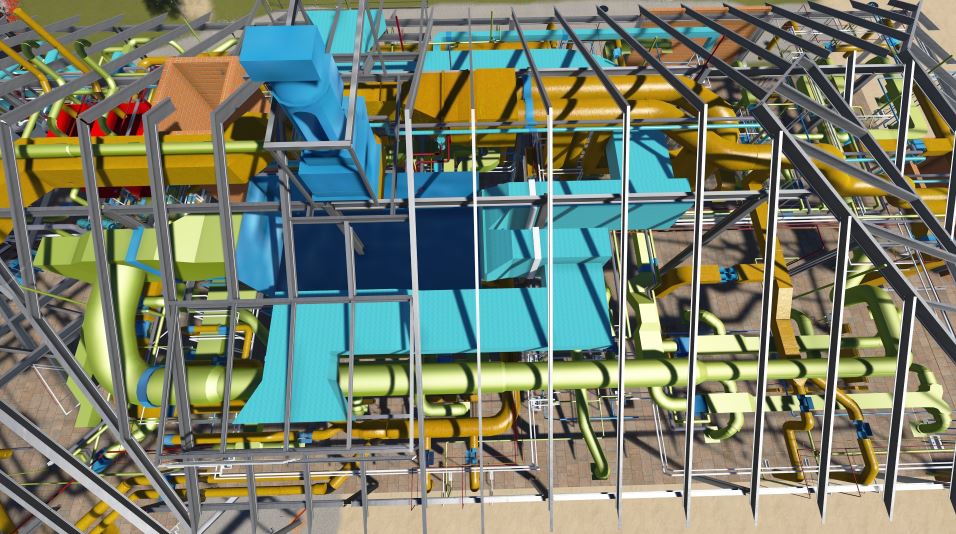
MEP Coordination Process: Typical Stages in MEP Coordination
Understanding the MEP Coordination Process: Typical Stages in MEP Coordination
The MEP coordination process is a comprehensive and structured approach that is vital for the successful integration of mechanical, electrical, plumbing, and fire protection systems in construction projects. It is imperative that all stakeholders adhere to the established protocols and timelines to ensure seamless coordination and avoid costly delays. Each discipline must be fully engaged, providing accurate and timely information, so that conflicts can be identified and resolved early in the design phase.
This proactive approach not only enhances efficiency but also minimizes rework and ensures compliance with regulatory standards. Failure to prioritize MEP coordination can result in significant project overruns, suboptimal system performance, and increased risk of future maintenance issues. Therefore, it is crucial for project managers to enforce strict adherence to the MEP coordination plan, holding all parties accountable for their contributions.
MEPF (Mechanical, Electrical, Plumbing, and Fire Protection) coordination is crucial in construction projects, especially in large-scale developments where various building systems must seamlessly integrate. to ensure the project’s success. Any misalignment or lack of coordination can lead to significant delays, increased costs, and potential safety hazards. It is imperative that all stakeholders—architects, engineers, contractors, and project managers—prioritize MEPF coordination from the project’s inception through to its completion. Clear communication channels must be established to facilitate real-time problem-solving and decision-making.
Utilizing advanced Building Information Modeling (BIM) technology is essential for detecting clashes and optimizing system layouts before actual construction begins. Regular coordination meetings should be scheduled to review progress, address issues promptly, and update plans as necessary.
Failure to adequately coordinate MEPF systems not only compromises the structural integrity but also affects operational efficiency and long-term maintenance of the building. Therefore, a rigorous approach towards MEPF integration is non-negotiable for achieving high-quality outcomes in any construction project.
3D models and shop drawings of mechanical, electrical, and plumbing systems are developed using software like Revit, AutoCAD MEP, or Navisworks. Care is taken to ensure the accuracy and completeness of these models, aligning them precisely with project specifications and adhering to industry standards. While the use of sophisticated software like Revit, AutoCAD MEP, and Navisworks is fundamental in creating these 3D models and shop drawings, it is imperative that all team members adhere strictly to established protocols. Any deviation from the project specifications or industry standards will not be tolerated.
We must prioritize precision and accountability at every stage of development to ensure the final product meets our high standards of quality. Furthermore, it’s essential for everyone involved to maintain clear communication channels and rigorous documentation practices. This will help us promptly address any discrepancies or issues that arise during the modeling process.
Thoroughness and meticulous attention to detail are non-negotiable elements of our workflow. We cannot afford lapses in accuracy or completeness; hence, regular reviews and audits will be conducted to guarantee compliance with all requirements. Each team member’s active participation in this process is crucial for achieving our collective goals efficiently and effectively.
Here is a detailed breakdown of the typical stages involved in MEP-BIM coordination, highlighting the importance and functionality of each phase:
Project Initiation:
This initial stage sets the groundwork for the entire coordination process. It involves defining project goals, scope, and deliverables. Crucially, this phase includes the development of a BIM Execution Plan (BEP), which outlines the project’s BIM strategy, standards, protocols, and milestones. It sets clear expectations for collaboration among all stakeholders.
MEP 3D Modeling:
At this stage, MEP engineers and designers use BIM software to create detailed 3D models of all MEP systems. These models include comprehensive data about the components and layout of mechanical, electrical, and plumbing systems. The accuracy of these models is critical as they form the basis for clash detection and resolution processes.
Clash Detection and Resolution:
Utilizing advanced BIM software, clashes between different systems (e.g., piping running into ductwork) are identified. This critical phase ensures that potential conflicts are resolved virtually before they can become real issues on site, saving time and costs associated with rework.
Coordination Meetings:
Regular coordination meetings are essential. These meetings involve architects, engineers, and other stakeholders. The purpose is to review the progress of the MEP modeling, discuss detected clashes, and agree on resolutions. Collaboration and communication during these meetings are key to ensuring that all teams are aligned and potential issues are addressed promptly.
Model Updates and Revisions:
Following coordination meetings, necessary revisions are made to the MEP models to reflect agreed-upon changes. This iterative process ensures that the model is continually refined to meet the project requirements precisely.
Validation and Verification:
Once the models are updated, they undergo a validation and verification process. This stage ensures that all systems are accurately represented and comply with the project specifications and regulatory requirements. It’s vital for maintaining the integrity of the design and ensuring functional efficiency.
Final Documentation:
Upon completion of the coordination and verification stages, final project documentation is prepared. This documentation includes detailed drawings, specifications, and supporting documents that guide the construction team during the actual build.
As-Built Documentation:
After the construction is complete, as-built documentation is created, reflecting the installed systems as they were actually built. This documentation is crucial for future maintenance, renovations, or expansions, providing a precise reference that details how the systems are installed and integrated within the building.
In conclusion, each stage of the MEP coordination process is critical and requires meticulous attention to detail, rigorous planning, and collaborative effort among all project stakeholders. This systematic approach ensures that the MEP systems are not only functional and efficient but also cost-effective, safe, and compliant with all necessary standards and regulations.
The Advantages of Using BIM in Precast Concrete Design
[…] significantly reduce errors and rework, as the comprehensive models allow for precise planning and coordination among all stakeholders involved in the construction process. This not only minimizes costly delays but also enhances overall project quality by ensuring that […]